woods
Well-Known Member
I guess I have been lucky in that running a Lee Collet through the necks sets the ID for my Forster mandrel. Sometimes it is indeed very tight but that can be good. You only have to turn once so I just force it in. Lubing does not seem to help. You can and I have chuck the mandrel in a drill and smooth the surface against some steel wool or fine sandpaper. I don't think I have actually taken off any of the diameter though.
Like I said, for me it is new brass turning. An indispensable tool IMO is a ball micrometer and a hands free stand
Then you need to go through some math. For instance if you have a tight necked chamber then you need to calculate what thickness you need to turn to in order to have the neck clearance you want on a loaded round. For instance on my 280AI I have a .313" neck
The Nosler 280 rem brass I use has a neck thickness of .0135" to .0145". So
.313"-.003"=.310"-.284"=.026"/2=.013"
So preliminarily I determine I have to turn to .013". That is a turn that will remove brass from the entire surface. So after setting the turner up so the case neck will go all the way onto the turning mandrel to the case mouth stop and turn all the way to the shoulder and a little onto the shoulder
there is a trial and error on setting the cutter to take off the exact amount you want and turn a little into the shoulder
After firing once I use pin gauges and the micrometer to check the dimensions. You have to allow for some springback and make adjustments. If I have do-nut development then Forster makes a reamer that will fit where the mandrel goes and you can trap the neck brass between the outside cutter and the inside reamer for very consistant neck thickness if you have .003" over caliber ID
Not a very complicated method of turning and there are other methods that may be more exact but it works for me.
A lot will depend upon your brass. If you have Lapua brass that has a neck thickness variance of .0005" or so and do not have a tight necked chamber then turning is unwarranted IMO. If you have brass that varies overall .002" or less then neck turning may be benficial and I would turn to the thinnest thickness. If you have brass that has more neck thickness variation than .002" then you need to sort the worst offenders and turn the ones that are the most consistant.
IMO neck turning has the biggest benefit when sizing with a bushing die. With a Lee Collet or expander ball type then turning is mostly wasted work.
YMMV
Like I said, for me it is new brass turning. An indispensable tool IMO is a ball micrometer and a hands free stand
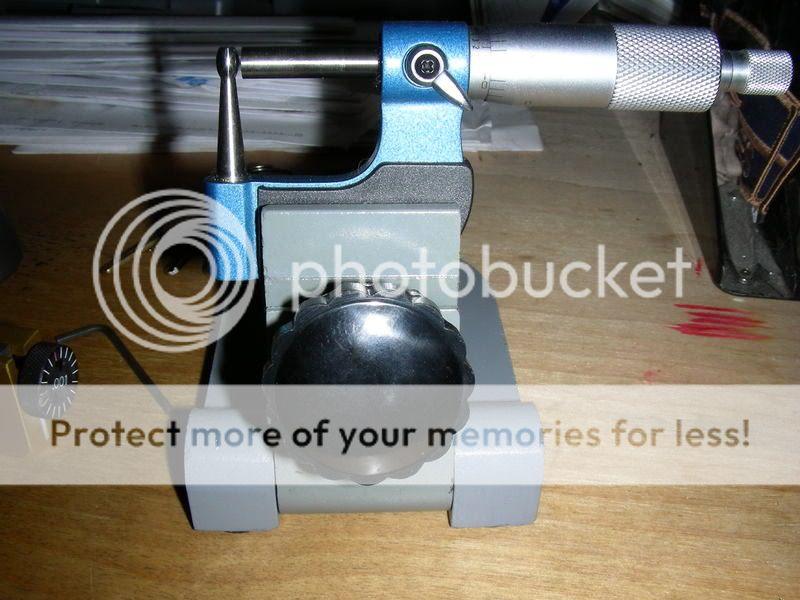
Then you need to go through some math. For instance if you have a tight necked chamber then you need to calculate what thickness you need to turn to in order to have the neck clearance you want on a loaded round. For instance on my 280AI I have a .313" neck
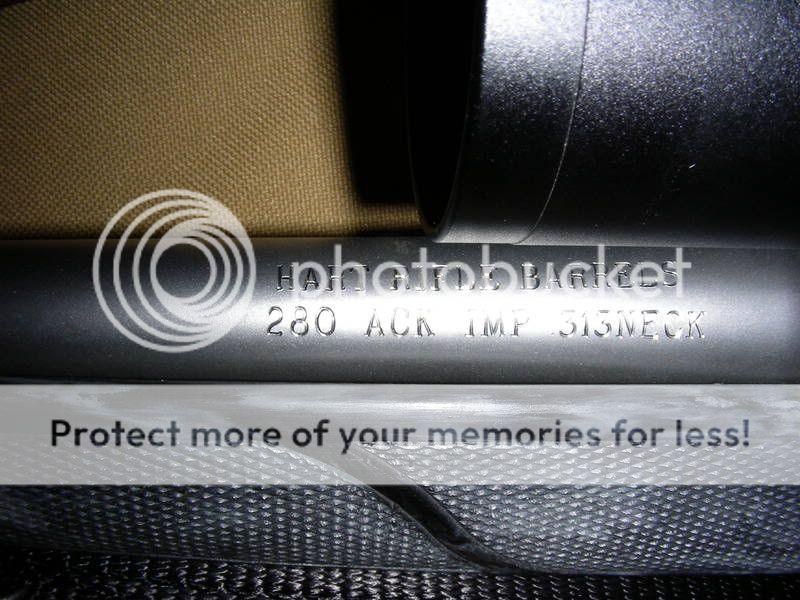
The Nosler 280 rem brass I use has a neck thickness of .0135" to .0145". So
.313"-.003"=.310"-.284"=.026"/2=.013"
So preliminarily I determine I have to turn to .013". That is a turn that will remove brass from the entire surface. So after setting the turner up so the case neck will go all the way onto the turning mandrel to the case mouth stop and turn all the way to the shoulder and a little onto the shoulder
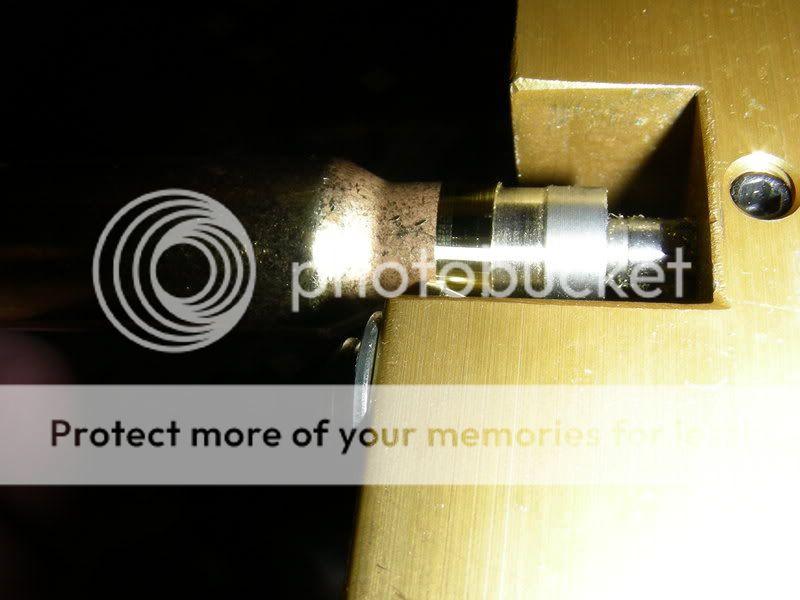
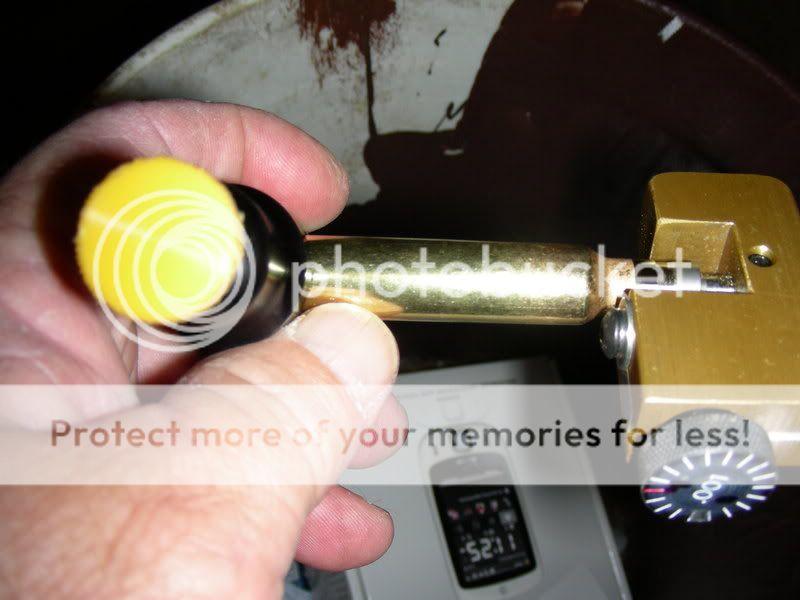
there is a trial and error on setting the cutter to take off the exact amount you want and turn a little into the shoulder
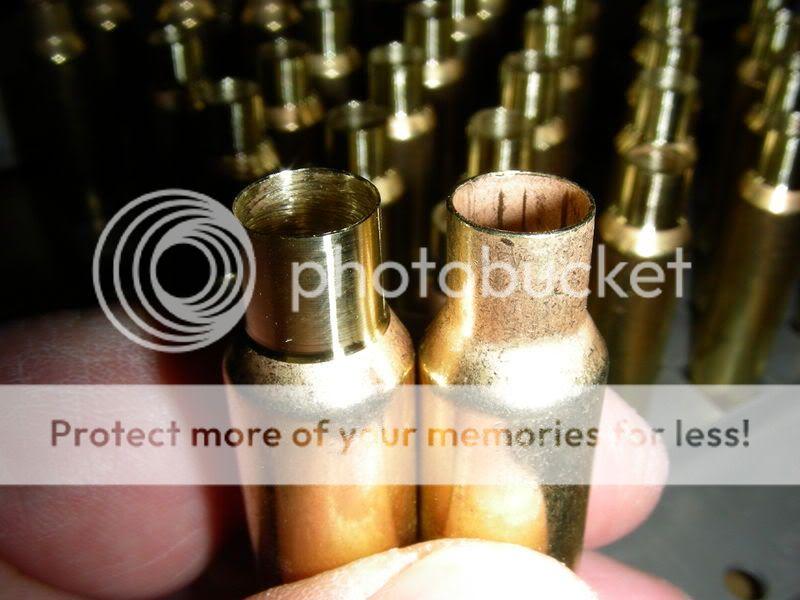
After firing once I use pin gauges and the micrometer to check the dimensions. You have to allow for some springback and make adjustments. If I have do-nut development then Forster makes a reamer that will fit where the mandrel goes and you can trap the neck brass between the outside cutter and the inside reamer for very consistant neck thickness if you have .003" over caliber ID
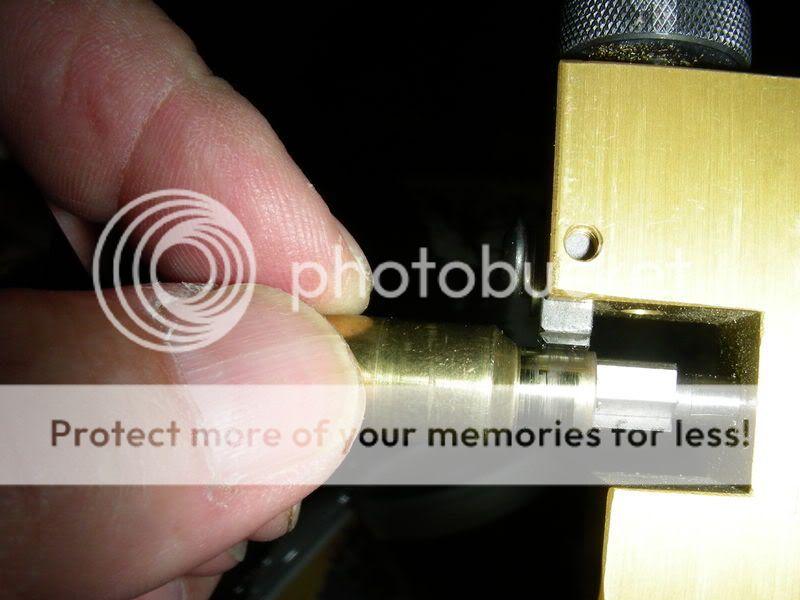
Not a very complicated method of turning and there are other methods that may be more exact but it works for me.
A lot will depend upon your brass. If you have Lapua brass that has a neck thickness variance of .0005" or so and do not have a tight necked chamber then turning is unwarranted IMO. If you have brass that varies overall .002" or less then neck turning may be benficial and I would turn to the thinnest thickness. If you have brass that has more neck thickness variation than .002" then you need to sort the worst offenders and turn the ones that are the most consistant.
IMO neck turning has the biggest benefit when sizing with a bushing die. With a Lee Collet or expander ball type then turning is mostly wasted work.
YMMV