AJ Peacock
Well-Known Member
I thought I'd document the process I use to reload LR rounds, as someone might be able to point out something I'm missing or do differently than they do. I don't claim any of this process as new/different or created by me. The steps in this process have ALL been documented in books (like "HandLoading for Competition" by Glen Zediker) and articles (like Jerry Teo's great article on this forum). These steps are just the ones I use and have found this process meets my needs.
Starting with new brass, I use a primer pocket uniformer in a cordless drill to make the primer pockets square on the bottom and consistent depths. I inspect each piece of brass at this point and toss any piece that looks odd in any way.
I then use a flash hole deburring tool. I use the Sinclair tool because it indexes against the inside of the cartridge head instead of the neck. The tools that index off the neck require brass that is identical in length to work correctly and I don't trim brass until after it's been fired at least once.
I then resize the brass. This rounds the necks, many times you will find that new brass has been beat up a bit in transit and the necks take the majority of the abuse. Although I full length resize, if the new brass will cycle in my rifle, I won't touch the shoulder at all. I use Redding full length bushing dies and only resize about 1/2 of the neck. I only use the expander ball on new brass (to make the necks round), I remove it from the die when resizing previously fired brass. I use Imperial sizing wax as a lubricant.
I wipe the resizing wax off of each piece of brass, using a paper towel.
Now that the necks are round, I'll lightly deburr the inside and outside of the necks. I use a VLD deburrer for the inside.
I then run a nylon brush in/out of the case necks several times to remove the residual sizing wax from inside the case necks. I clean the nylon brush every 10 cases or so by simply squeezing it in and rolling it around on a paper towel.
I'll prime the brass using a Lee or RCBS hand priming tool.
I use an RCBS chargmaster to throw/weigh each charge. I always calibrate the scale before I use it.
Seating the bullet. I have found that seating the bullet very slowly and rotating it a 1/3 of a rotation a couple times during the initial 1/2 of the seating operation helps with runout.
For example I'll seat the bullet 1/10" and rotate 1/3 turn in the shell holder, then another 1/10", then rotate again and then slowly seat the bullet the rest of the way. Although I have no way to prove it, I think that slowly and gently seating the bullet, allows the bullet to slide into the neck without deforming the concentricity of the neck/shoulder junction.
I then measure the concentricity and seperate the loaded rounds into 3 piles. 1) those with less than .0005" runout. 2) those with less than .002" runout but more than .0005" 3) those with more than .002" runout.
I keep the rounds segregated in my ammo boxes and use those with most runout as foulers and for fun shooting. The others are used as needed. I mark the worst ones with a sharpie marker. A small mark on the primer denotes the shells with the most runout.
There are a couple differences when I reload already fired brass. I remove the expander button from my dies and only resize about 1/2 of the neck. I believe the other 1/2 of the neck will help orient the case into the center of the chamber. I also adjust my sizing die to move the shoulder of the cartridges back about .001" from a crush fit. I've been told that a crush fit is the way to go, but I haven't had consistent results with it. Once I figure out how much to push the shoulder back, I'll write it down in my log and duplicate it with future loads using a Hornady headspace gauge and calipers.
I will also trim the entire lot of brass to the same length which will square the necks. I trim after the first firing and then keep an eye on the length of the brass and trim as required. I have been told that the length isn't as important as the squareness. After trimming, the inside and outside of the neck must be deburred again.
I've made one change to my presses that helps with concentric ammo. That change is removing the C-clip that holds the shellholder in place. I let the shellholder float in the slot, this keeps the shellholder/shell from being forced off center. Some folks will put an O-ring around the slot to keep the shell holder 'in the press', but I've found it is not needed and more trouble than it's worth.
Here are the tools I use to prep the brass. cordless drill with Sinclair primer pocket uniformer, Sinclair flash hole deburrer, Nylon brush, Sinclair VLD inside neck deburring tool, outside neck deburring tool.
Thats about it.
AJ
Starting with new brass, I use a primer pocket uniformer in a cordless drill to make the primer pockets square on the bottom and consistent depths. I inspect each piece of brass at this point and toss any piece that looks odd in any way.
I then use a flash hole deburring tool. I use the Sinclair tool because it indexes against the inside of the cartridge head instead of the neck. The tools that index off the neck require brass that is identical in length to work correctly and I don't trim brass until after it's been fired at least once.
I then resize the brass. This rounds the necks, many times you will find that new brass has been beat up a bit in transit and the necks take the majority of the abuse. Although I full length resize, if the new brass will cycle in my rifle, I won't touch the shoulder at all. I use Redding full length bushing dies and only resize about 1/2 of the neck. I only use the expander ball on new brass (to make the necks round), I remove it from the die when resizing previously fired brass. I use Imperial sizing wax as a lubricant.
I wipe the resizing wax off of each piece of brass, using a paper towel.
Now that the necks are round, I'll lightly deburr the inside and outside of the necks. I use a VLD deburrer for the inside.
I then run a nylon brush in/out of the case necks several times to remove the residual sizing wax from inside the case necks. I clean the nylon brush every 10 cases or so by simply squeezing it in and rolling it around on a paper towel.
I'll prime the brass using a Lee or RCBS hand priming tool.
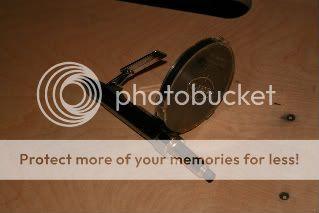
I use an RCBS chargmaster to throw/weigh each charge. I always calibrate the scale before I use it.

Seating the bullet. I have found that seating the bullet very slowly and rotating it a 1/3 of a rotation a couple times during the initial 1/2 of the seating operation helps with runout.
For example I'll seat the bullet 1/10" and rotate 1/3 turn in the shell holder, then another 1/10", then rotate again and then slowly seat the bullet the rest of the way. Although I have no way to prove it, I think that slowly and gently seating the bullet, allows the bullet to slide into the neck without deforming the concentricity of the neck/shoulder junction.
I then measure the concentricity and seperate the loaded rounds into 3 piles. 1) those with less than .0005" runout. 2) those with less than .002" runout but more than .0005" 3) those with more than .002" runout.
I keep the rounds segregated in my ammo boxes and use those with most runout as foulers and for fun shooting. The others are used as needed. I mark the worst ones with a sharpie marker. A small mark on the primer denotes the shells with the most runout.
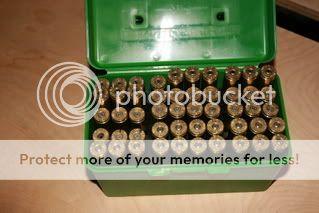
There are a couple differences when I reload already fired brass. I remove the expander button from my dies and only resize about 1/2 of the neck. I believe the other 1/2 of the neck will help orient the case into the center of the chamber. I also adjust my sizing die to move the shoulder of the cartridges back about .001" from a crush fit. I've been told that a crush fit is the way to go, but I haven't had consistent results with it. Once I figure out how much to push the shoulder back, I'll write it down in my log and duplicate it with future loads using a Hornady headspace gauge and calipers.
I will also trim the entire lot of brass to the same length which will square the necks. I trim after the first firing and then keep an eye on the length of the brass and trim as required. I have been told that the length isn't as important as the squareness. After trimming, the inside and outside of the neck must be deburred again.
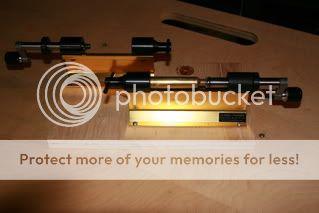
I've made one change to my presses that helps with concentric ammo. That change is removing the C-clip that holds the shellholder in place. I let the shellholder float in the slot, this keeps the shellholder/shell from being forced off center. Some folks will put an O-ring around the slot to keep the shell holder 'in the press', but I've found it is not needed and more trouble than it's worth.
Here are the tools I use to prep the brass. cordless drill with Sinclair primer pocket uniformer, Sinclair flash hole deburrer, Nylon brush, Sinclair VLD inside neck deburring tool, outside neck deburring tool.
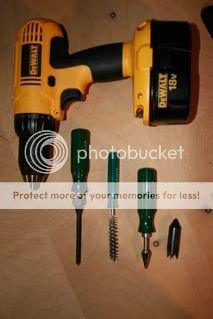
Thats about it.
AJ
Last edited: