gunlover05
Well-Known Member
- Joined
- Sep 23, 2015
- Messages
- 46
So I decided to make my own brass annealing machine, but didn't want to take the time to order a bunch of parts such as motors, ac/dc converters, and controllers. I'm not a high volume reloader, so it didn't have to be fully automatic. But having consistent time on the flame is important as I learned. So I watched a lot of youtube videos on annealing machines, and decided to make my own powered by my cordless drill, using gear reduction principles. I did buy a $5 lazy susan bearing from ace hardware. Pardon the mess on my bench too
.
I put some nonslip tape on the back of the 9" cake pan, and some gorilla tape on the drill chuck to grip better. I used a pipe clap to control the speed of the drill, which was on the low speed setting, and I can just hold it against the back of the pan to power the pan. Most everything I had in my garage to build it, except the cake pan ($8). below is a short youtube clip of a few cycles. I'm sure there are easier ways, but it was fun to build on a cold winter weekend.
https://www.youtube.com/watch?v=K6sm4cmNADw

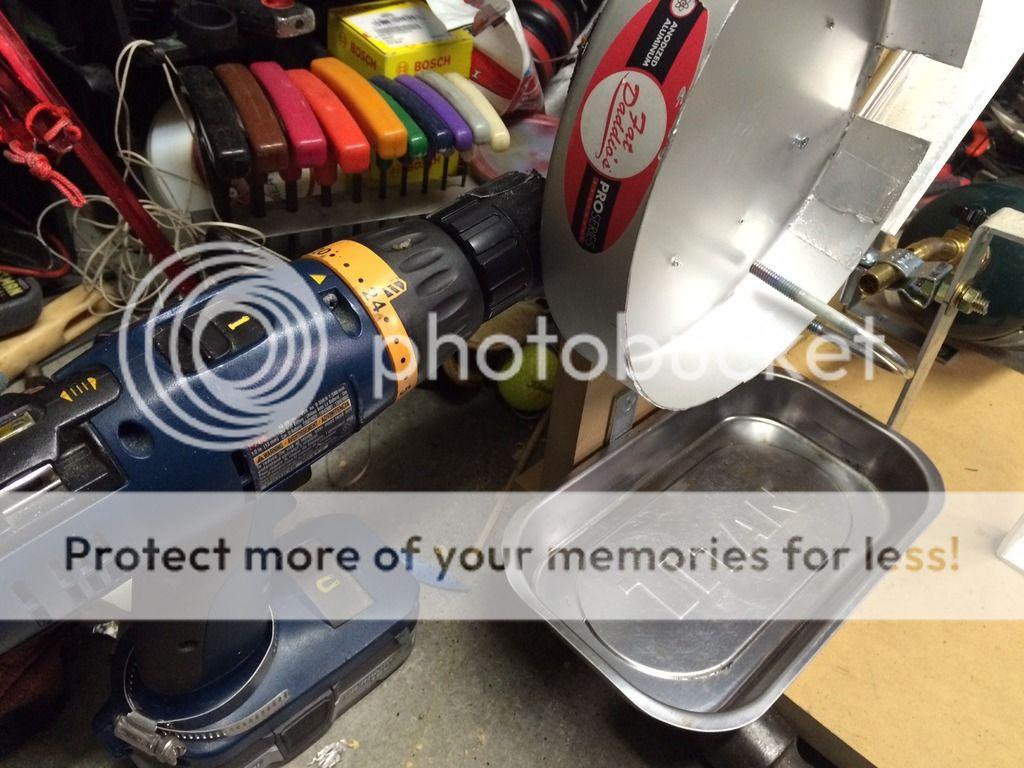
I put some nonslip tape on the back of the 9" cake pan, and some gorilla tape on the drill chuck to grip better. I used a pipe clap to control the speed of the drill, which was on the low speed setting, and I can just hold it against the back of the pan to power the pan. Most everything I had in my garage to build it, except the cake pan ($8). below is a short youtube clip of a few cycles. I'm sure there are easier ways, but it was fun to build on a cold winter weekend.
https://www.youtube.com/watch?v=K6sm4cmNADw

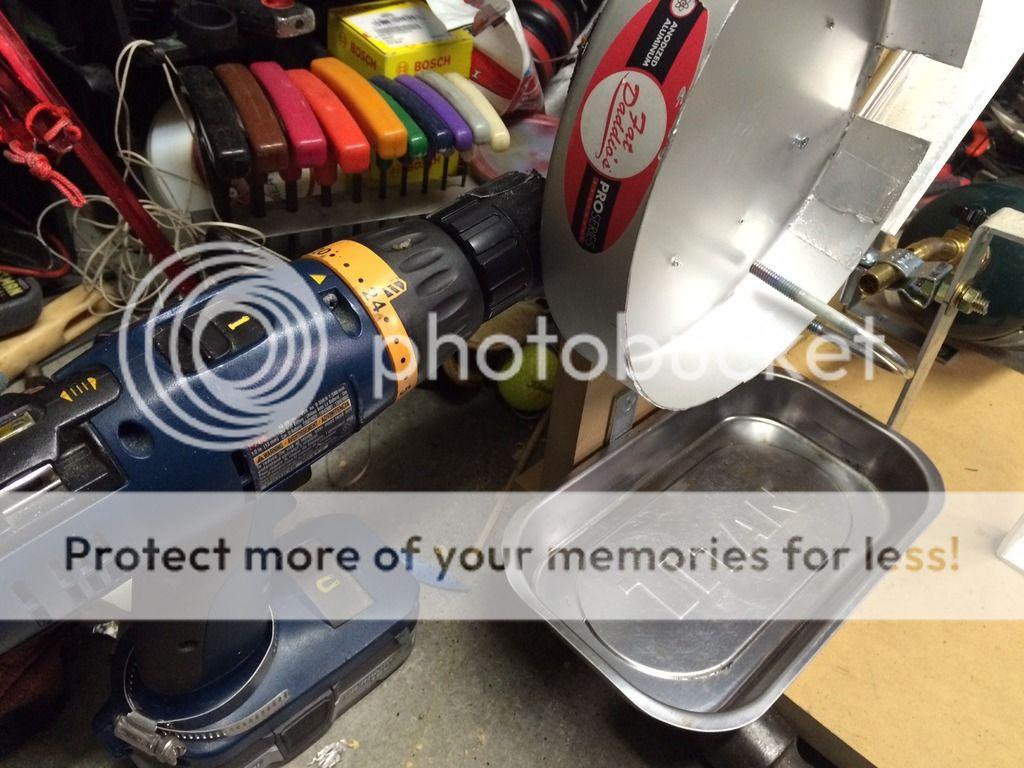
Last edited: