bigtoy302
Active Member
So this is my first rifle project. I will be doing all the work to the rifle myself. I am not a gunsmith but a machinist with just enough knowledge to hurt something. I am sure I will be doing some stuff differently from some of you real gunsmiths, but like I said before this is all new to me. Don't be affriad to comment on my ways of doing things. I am always up for new ideas. I am starting with a Remington 700 VS in .22-250. Specs for this build.
.300wsm
Factory hs-stock
blueprinted action and bolt
Sako extractor
Wyatt's extended mag box
28" Shilen select match grade stainless barrel #17 contour
muzzle brake
Badger recoil lug
Nightforce nsx 5.5x22x50 mil-dot
nightforce steel rings
Nightforce 20 moa base.
first I made a cat head for the action and ground a .7018 arbor to fit snuggly into the action. I chucked it up, dialed it in and faced the front and the bolt lug face.
Then I used my indicator to fid the center of the threads, then cleaned them up
Ryan
.300wsm
Factory hs-stock
blueprinted action and bolt
Sako extractor
Wyatt's extended mag box
28" Shilen select match grade stainless barrel #17 contour
muzzle brake
Badger recoil lug
Nightforce nsx 5.5x22x50 mil-dot
nightforce steel rings
Nightforce 20 moa base.
first I made a cat head for the action and ground a .7018 arbor to fit snuggly into the action. I chucked it up, dialed it in and faced the front and the bolt lug face.
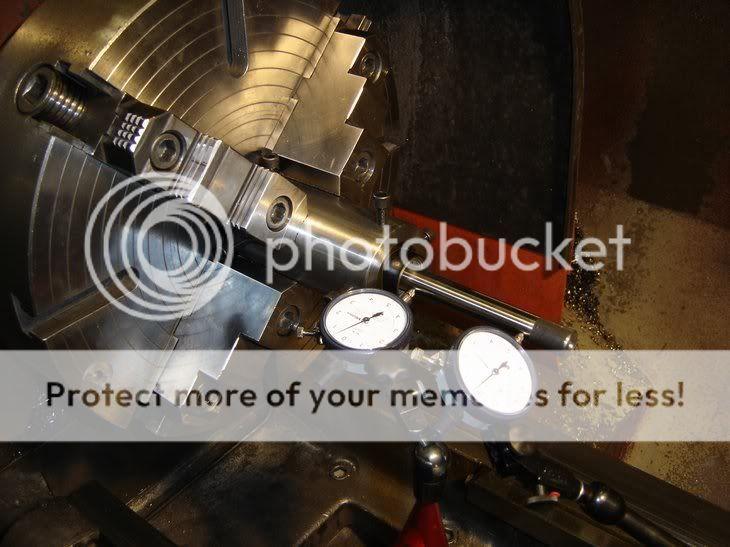

Then I used my indicator to fid the center of the threads, then cleaned them up
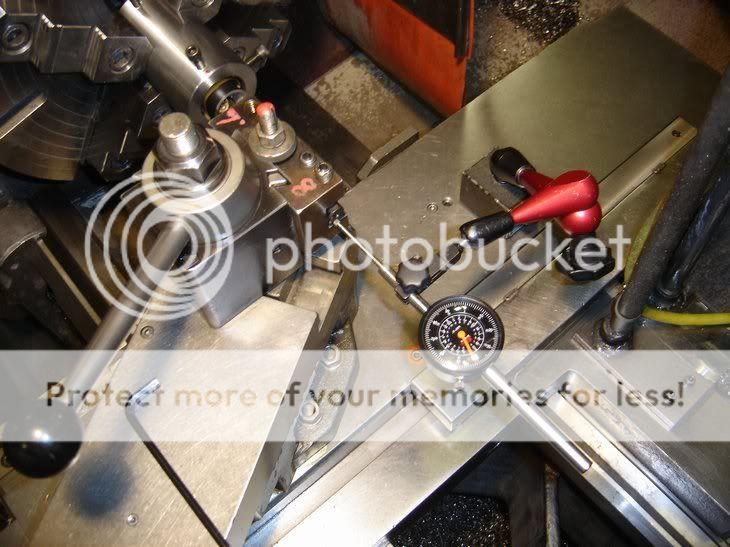
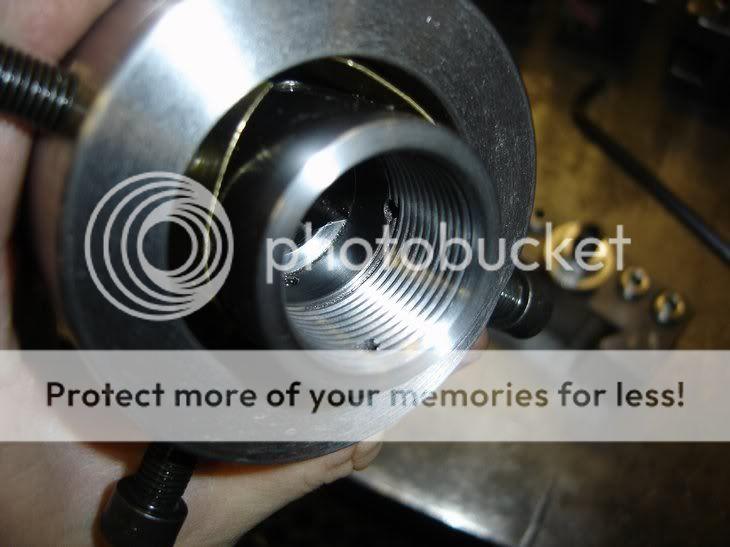
Ryan
Last edited: